POPAI AWARDS – 10 Awards
On 23rd November, there were announced the POPAI Awards for the best advertising means in the sphere of in-store communication for the year 2017. We won awards for six of our projects that evening. The most successful was o…
The deer origami from Jägermeister lures to the autumn atmosphere
For Jägermeister, the herbal liqueur brand, we have created an unconventional and attractive display with a deer „origami“. It is intended for the autumn action of the Czech stores of the Globus and Slovakian Metro chains….
Reflections of summer on Pinterest
Realizations and designs that have attracted us and could appeal to you as well.
These and many other worldwide POP inspirations can be continually found on DAGO Pinterest.
We support children and seniors
We are not alone in the world. It is human and natural to help others, especially to people who can´t help themselves. We, therefore, decided to contribute with 250,000 CZK to several projects this year that we think are ve…
Purina by Nestlé celebrated the Day of Cats with customers of Globus stores
Purina brand of food for animals of the company Nestlé celebrated the Day of Cats at the beginning of August this year. In Globus stores, we prepared original playful display, together with Nestlé, attracting to a long-term…
Nestlé case study: reflecting the buying behaviour is the key opportunity of the confectionery category growth.
Confectionery is a fixed star in shopping carts, but its producers have faced an important challenge in recent years: How to ensure a long-term and especially healthy growth for this category? In recent years, its sales hav…
Gold at POPAI Awards Paris with Kofola
In the category ”Drinks” of the prestigious European competition POPAI Awards Paris, we won a gold medal together with our client Kofola for the realization of a pallet island for the Rajec brand. Our other three projects w…
Fresh Pinterest goodies
]
And again, we bring you some of the interesting realizations found on Pinterest. This time with the Christmas theme.
These realizations and many others can be found o…
Globalshop Las Vegas 2017: top class traditional solutions
25th Globalshop Las Vegas 2017 (www.globalshop.org) was organized in the spirit of “Experience Defines You”; so the customer experience was traditionally the priority.
Compared to Euroshop Düsseldorf, this U.S. Trade Fair w…
LG trendy shopping in Alza
Together with the LG Electronics brand, we created another interesting project. On the 42 square meters of the Prague Alza Showroom, we participated in the creation of the fully functional shop-in-shop presenting several ty…
The new software will reduce order processing times by up to three quarters
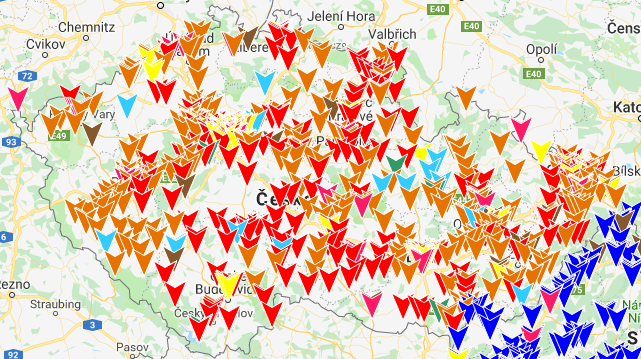
Production in the P.O.S. segment is very complex and many subjects cooperate within it. For a long time already we have wondered how to manage our individual projects more effectively – from the production itself to the product placement in stores. That is why we started to develop our own software, which will bring all the production attributes together and make it easier to everyone involved in preparations of individual orders – clients, suppliers and our internal teams.
After the development phase, which lasted for one and a half year, we are now testing the new software. And so far, we have been very successful with it. It turns out that a unified project management facilitates work for us as well as for our customers.
The system constantly transfers all actual data to clients and their business representatives – data about all their displays, where they are located, detailed information about each store, installation plan and so on. If it is found that there is something wrong with any product, they can report the problem using the software and take a photo of its current status using a mobile phone or tablet and upload the image into a cloud.
The time necessary to complete a project rapidly shortens
The system reports the need for ordering appropriate items on time according to warehouse stock and budget and related expenses. It can also accept an order from an information system of a client. So this reduces downtime, which otherwise normally occurs and also the burden of all participating elements because the system automates many activities throughout the implementation process. Stores with installed products are displayed on a map for better clarity; of course it is possible to generate reports and schemes. With regards to data collection in stores, the number and type of monitored P.O.P. media displays in each store is always clear. Thus there is no need for a classic stocktaking, which is now continual. For easier orientation, the products can be filtered according to locality, material, store type, sales representatives and other parameters. Sales representatives and installation technicians have an access to the system available all the time and they can view actual data in certain location using GPS. They should also update information on the spot.
While previously, for example, the placement of three thousand large checkout zones took two or three years, with the new system we can do it in six months. The big advantage is the absolute overview of the installed materials, which enables also repair management and inspection.
10 clients have been participating in the testing and their feedback is very positive. They consider the acceleration of the whole order processing to be the main advantage. Clients have an overview of everything important and approve particular steps just on-line. We see the future in the industry in the closer integration of our comprehensive services with client needs and we are glad that we can already participate in the realization of this vision.
Marek Koncitik and Your DAGO team