Smart display can mix drinks
]
Mixed drinks and spirits belong to each other. So why don´t we offer recipes how to prepare the right cocktail to our customers directly in a store? Thanks to the new…
Our victory in POPAI AWARDS 2014
Nine – that is just the exact number of times we won awards for our P.O.P. applications registered for the international competition for the best communication means and advertisements at points of sales POPAI AWARDS. The pro…
Unique P.O.P. for M&M´s in TESCO
Creating a unique P.O.P. application for sweets is not easy. Shoppers often do not plan buying these products that end up in shopping carts as the r
Shop in shop ACER for Alza
How to attract customers not to be afraid to try all displayed technologies of the Acer brand in a store with electronics and perhaps even buy them? We bet on spacious and elegant shop-in-shop.
The company Acer used the ac…
JOJO shop-in-shop in TESCO
In August, Nestle gave us the opportunity to create specific shop-in-shops for the popular brand of JOJO candies. So in Czech Tesco stores, there is being created a specific candy world, which will attract customers at firs…
Czech World of Grilling 2
The company Groupe Bongrain, in co-operation with our company, built on the last year´s successful campaign of the Czech World of Grilling as it, again this year, prepared grilling themed promo-spots for customers of Inters…
Top Class Shop in Shop Becherovka
Our new shop-in-shops for Becherovka increase sales at the Prague Airport in six Aelia Duty Free shops
Shoppers in duty free shops Aelia at the Václav Havel Airport have the chance to get something typical Czech at the last…
Imperial Tobacco illuminating displays
Actually we came up with an elegant and simple solution how to attract potential customers of the Imperial Tobacco brand immediately when entering the store. For our client, we designed, produced and installed new lighting…
Euroshop 2014 – a sci-fi reality
Our business is extremely changing and developing. A clear evidence of that was this year´s retail trade fair Euroshop 2014. Several members of our DAGO team have visited it traditionally and so we can share our impressions…
Demo walls for mobile phones in Electroworld
Our lighting walls for mobile phones remind a child´s puzzle. With several clicks on a controller, it is possible to change their colour and it is also easy to change a brand logo. Entire transformation of an actual mobile-…
The new software will reduce order processing times by up to three quarters
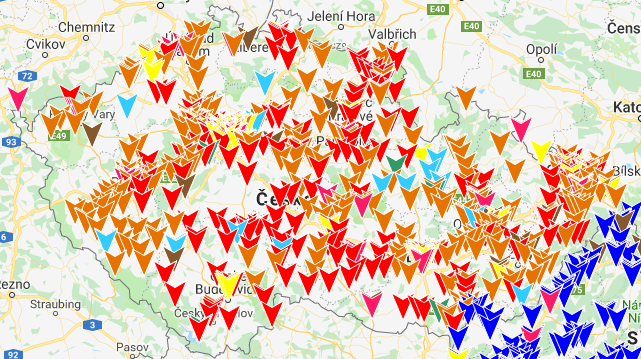
Production in the P.O.S. segment is very complex and many subjects cooperate within it. For a long time already we have wondered how to manage our individual projects more effectively – from the production itself to the product placement in stores. That is why we started to develop our own software, which will bring all the production attributes together and make it easier to everyone involved in preparations of individual orders – clients, suppliers and our internal teams.
After the development phase, which lasted for one and a half year, we are now testing the new software. And so far, we have been very successful with it. It turns out that a unified project management facilitates work for us as well as for our customers.
The system constantly transfers all actual data to clients and their business representatives – data about all their displays, where they are located, detailed information about each store, installation plan and so on. If it is found that there is something wrong with any product, they can report the problem using the software and take a photo of its current status using a mobile phone or tablet and upload the image into a cloud.
The time necessary to complete a project rapidly shortens
The system reports the need for ordering appropriate items on time according to warehouse stock and budget and related expenses. It can also accept an order from an information system of a client. So this reduces downtime, which otherwise normally occurs and also the burden of all participating elements because the system automates many activities throughout the implementation process. Stores with installed products are displayed on a map for better clarity; of course it is possible to generate reports and schemes. With regards to data collection in stores, the number and type of monitored P.O.P. media displays in each store is always clear. Thus there is no need for a classic stocktaking, which is now continual. For easier orientation, the products can be filtered according to locality, material, store type, sales representatives and other parameters. Sales representatives and installation technicians have an access to the system available all the time and they can view actual data in certain location using GPS. They should also update information on the spot.
While previously, for example, the placement of three thousand large checkout zones took two or three years, with the new system we can do it in six months. The big advantage is the absolute overview of the installed materials, which enables also repair management and inspection.
10 clients have been participating in the testing and their feedback is very positive. They consider the acceleration of the whole order processing to be the main advantage. Clients have an overview of everything important and approve particular steps just on-line. We see the future in the industry in the closer integration of our comprehensive services with client needs and we are glad that we can already participate in the realization of this vision.
Marek Koncitik and Your DAGO team